No matter the industry, all warehouse tenants have at least one thing in common: a need for a well-maintained facility. That’s why a complete move-out inspection is so important.
In addition to ensuring that you’re leaving a clean and functional building for the next tenant, an end-of-lease walk-through can also help you identify any repairs you may be expected to perform or damage you’ll need to pay for.
1. Loading dock
No matter what it is you’re storing or shipping, your merchandise will enter and exit through the loading dock, which means it will have the usual wear and tear. But what if it’s more than a few dings and scrapes? To begin your loading dock inspection, check the concrete on the exterior of the building:
- Is it crumbling?
- Are the bumpers still present and intact?
If dock bumpers begin to deteriorate or fall off altogether, it’s very easy for trucks to damage the exterior of the building. Once the concrete around the dock begins to erode, replacing any of the equipment embedded into the dock becomes much more difficult.
Next, move up to the loading zone:
- Does the dock door open as it should?
- Are the tracks in good condition with no dents or damage?
- Does the dock leveler and lip function well?
Unreliable dock doors slow down processes and present safety concerns. If the lip of the dock leveler doesn’t extend properly, or if the unit moves too slowly or only with extra force, your facility owner may request you invest in maintenance. He or she won’t want the next tenants to have to manually position the leveler, putting their fingers and hands in harm’s way.
2. Offices
Every industrial work environment needs a tidy, professional office for the administrative side of the business, so make sure you’re leaving your office space with clean walls, unstained carpets and functional windows. If you notice that certain equipment, such as the HVAC or the refrigerator in the break room, are beginning to fail, inspect them and make any necessary repairs.
3. Racking
While every business needs storage, not all tenants of a building will need the same type of storage system. Have you spoken to the facility owner to determine whether you can leave any unneeded racking behind? Find out if you’ll need to arrange for your racking system to be removed. If this is the case, make sure the floor beneath is in good condition so the following tenants can utilize the space safely.
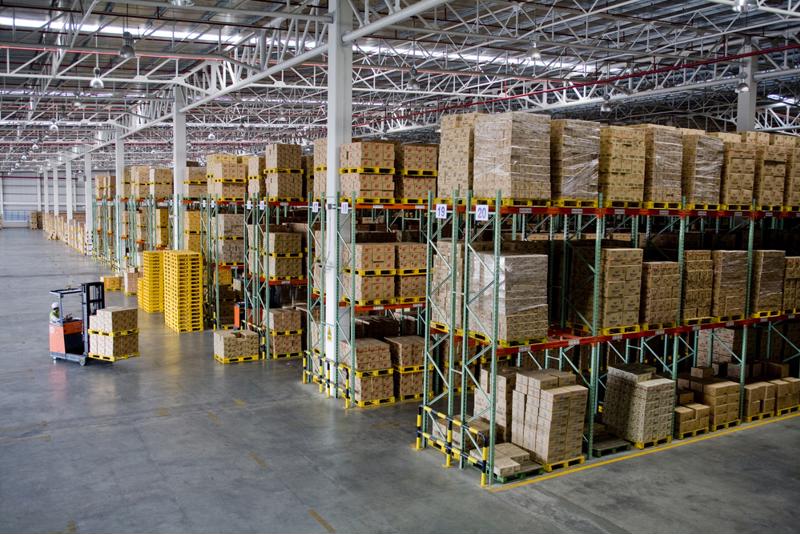
If you’re leaving your racking system for the next company to use, be sure it’s reliable. If any columns or posts are dented or cracked, repair or replace them. If you have guards around the columns or lining the bottom of the shelves for protection, make sure these, too, are intact. Review your accident records and connect incidents with damage as best as you can. If a forklift ran into the guard and left a dent, there’s a chance that the beams behind it also sustained damage.
4. Other equipment
If you’ve been at your location a while, then you’ve probably personalized your space to meet your needs, so determine which assets will be coming with you to your next location and which will stay behind in your former facility. If you’re leaving behind equipment for the next tenant to take advantage of, make sure it’s in good condition. You may find that a few repairs go a long way toward making that asset more friendly to the next user.
Having a set of second eyes and helping hands during your move-out inspection can help identify problem areas and avoid surprises. Miner’s professionals can help. For advice about building or equipment maintenance and repairs during your move, reach out to Miner.