LOADING DOCK Safety
Safeguard employees on your loading dock with equipment, policies and best practices.
UNDERSTAND THE IMPORTANCE OF LOADING DOCK SAFETY
As the operator of a commercial building, you are responsible for creating a safe environment for your employees. This rings especially true on the loading dock, where workers commonly perform their tasks alongside powered forklift trucks on elevated platforms, dealing with heavy equipment.
Dock accidents can be devastating for everyone involved. Enforcing loading dock safety practices gives you the best chance of preventing these incidents and keeping a spotless safety record. These are essential for getting into compliance with Occupational Safety and Health Administration (OSHA) regulations, but those rules are just the start — an ideal dock safety program goes beyond the baseline.
There are a variety of steps you can take to promote loading dock safety. Many of these involve equipment — the selection, installation, maintenance and repair of dock equipment such as dock plates, vehicle restraint systems and overhead door assets can reduce potential hazards. Others deal with the human element, with safety training keeping your workers aware of risks.
The ideal strategy for safety in the loading dock area will combine all these methods and more, generating a true culture of safety for your facility. The benefits of such an approach are numerous, because safety awareness and productivity tend to go hand in hand.
LOADING DOCK SAFETY: WHAT DOES OSHA REQUIRE?
OSHA requirements around the loading dock area are relatively straightforward. They are the bedrock on which more sophisticated worker safety programs are based. The agency’s main stipulation about all work environments is that the area must be safe and healthy for employees to complete their tasks.
Around the loading dock, this can mean setting up fall protection railings around the dock edge to prevent injuries caused by accidental slips. Pedestrian safety for loading dock workers can also involve mapping out safe paths for employees on foot and lanes for forklift truck operators.
Specific areas with their own OSHA regulations include forklift trucks. These regulations also encompass standards for loading and unloading trucks, trailers and train cars at the loading dock.
The safe operation of forklifts depends on several factors, with OSHA specifying in rules and clarifying letters that a forklift operator must be trained to use the vehicle effectively.
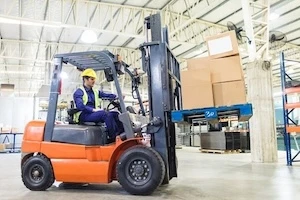
Trucks, trailers and train cars being loaded or unloaded need to have vehicle restraints in place to keep them from moving unexpectedly away from the loading dock. Wheel chocks are a minimum, and more advanced systems are available.
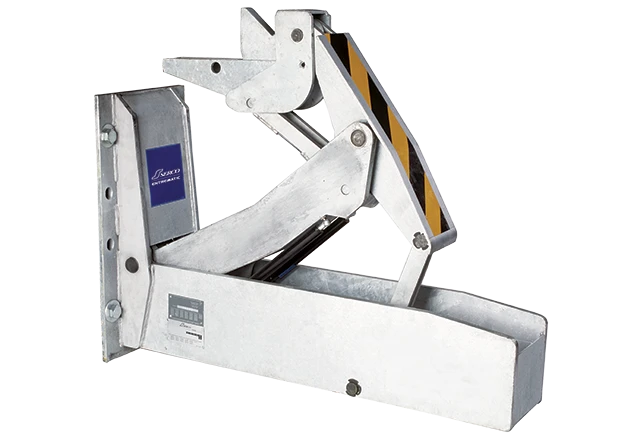
All loading dock equipment used to bridge the gap between trailers and the dock itself must have the capacity and endurance to handle the loads that pass over them, including both forklift trucks and cargo.
By following OSHA regulations, you can guard your loading dock and workers against a variety of hazards. However, these rules are more of a starting point than a comprehensive guide. Other loading dock safety tips can take you beyond basic compliance to create a more secure facility overall.
Quick Tips: Loading Dock Safety Musts
Meeting and exceeding OSHA requirements around loading dock safety means following common-sense principles. These include:
- Training all employees: Everyone working on or near the dock should understand their responsibilities,
- Overseeing forklift operations: All forklift operators need training on the vehicles, and the environment should contain controls like warning paint and safety lips to guard against falls.
- Managing dock plates and levelers effectively: Employees must know the capacity of dock plates and levelers and secure equipment firmly in place whenever it’s used.
- Cleaning and drying dock surfaces: Frequent attention to the dock surface is important to prevent slip-and-fall hazards, and the area should always be clear of debris.
- Securing vehicles: Essential safety considerations around trucks include the use of vehicle restraints and the segregation of pedestrian and automotive areas.
Start Right Now!
Start Right Now!
WHY FOCUS ON LOADING DOCK SAFETY AWARENESS?
An enhanced focus on loading dock safety practices can have wide-reaching effects on your employees. The commonly cited industry data holds that 25% of industrial accidents occur on loading docks, and reducing the incidence rate of these incidents is a powerful way to keep your team healthy, happy and effective.
The suffering associated with loading dock injuries is self-evident, and preventing these occurrences should be a top priority for every facility operator. It’s also worth noting that even incidents where no one is hurt can have a negative impact on overall performance.
When equipment suffers an unexpected breakdown or failure, that can bring productivity on the loading dock to a halt. The whole supply chain can suffer delays as workers attempt to resolve the issue. Therefore, increasing the reliability of equipment and preventing unexpected downtime is relevant from both personal safety and logistics productivity perspectives.
It pays to consider safety from an employee morale perspective. Workers gravitate to workplaces where their safety and comfort are priorities. A facility that doesn’t display clear consideration for its employees can have trouble attracting and retaining top performers, leading to further productivity issues.
There are numerous ways to build loading dock safety awareness, each capable of having a powerful impact on the effectiveness of your loading dock crew. Some of these focus on your people — training, preparation and day-to-day leadership are key elements in worker safety. Others revolve around equipment. When you have suitable, well-installed, properly maintained equipment, safety comes naturally.
LOADING DOCK SAFETY AWARENESS BEST PRACTICES: WHAT SHOULD YOU KNOW?
While the exact methods of keeping workers safe in the loading dock area will vary between facilities, there are a few loading dock safety tips that apply universally. For example, there is a reliable procedure that can help you detect and correct any potential hazards around your facility.
This methodology encompasses:
Taking stock of your current loading dock safety is important. What practices are in place? Are you using fall prevention systems on all ledges? Is the equipment in place suitable for its intended use? These questions and more can guide you through the process of improving loading dock safety.
One of the most basic but impactful practices to apply in the dock involves cleaning up any obstructions. Clear — and clearly marked — paths for both powered forklift vehicles and employees on foot are critical for safe movement. The area should also be dry to avoid slip-and-fall hazards. Dock seals and shelters can help in this regard.
A proactive maintenance program for all your equipment, paired with emergency repair services as needed, can keep your personnel safe and efficient. Using data-based insights to maintain equipment before it suffers a breakdown is a key way to prevent unplanned downtime and dangerous incidents.
Every worker who serves near the loading dock should receive training that applies to their specific role. For instance, forklift operators must know how to safely operate their vehicles in a variety of circumstances and shift supervisors should understand how to verify their team members are following correct practices.
Creating a safer loading dock area relies on a combination of people, processes and equipment. When you have an expert service provider on your side, it’s simpler to achieve this overall level of excellence and keep your facility running smoothly.
FIND A LOADING DOCK REPAIR PROVIDER NEAR YOU
FIND A LOADING DOCK REPAIR PROVIDER NEAR YOU
GET STARTED CREATING A SAFER LOADING DOCK
As a national service provider, MINER can make significant contributions to safety-promoting features around your loading docks. When every piece of loading dock equipment has been chosen to meet your needs, installed professionally, and maintained frequently, you’re set up for success. MINER’s factory-trained technicians can also provide emergency repair service as needed.
A loading dock outfitted with the right equipment is ideally prepared for day-to-day safety and is, therefore also a key element in employee engagement and morale. Every asset, from loading dock levelers to commercial doors and dock seals, deserves attention. With MINER, you have access to the best options from a variety of top original equipment manufacturers.
AT A GLANCE: FREQUENTLY ASKED QUESTIONS
OSHA’s standard regulations around facility safety apply on the loading dock. Relevant rules include the need to guard against falls, closely monitor forklift use and maintain all equipment.
The constant movement of people, vehicles and heavy loads on the dock is a risk factor. It’s important to ensure people and vehicles all have space to maneuver safely, and that equipment is capable of standing up to the weight it will carry each day.
To improve loading dock safety on a day-to-day basis, it’s important to focus on issues such as debris scattered on the dock area or wet floors. Keeping paths clear for employees can reduce the chance of a workplace accident.
Loading dock equipment that fails unexpectedly is a major risk factor. This means proactive maintenance can play a large role in overall safety and preparedness.