Warehouse Guard Rails
Maintain a safe and compliant warehouse environment with secure guard rail equipment.
ENHANCE SAFETY AWARENESS WITH WAREHOUSE GUARD RAILS FROM MINER
Wherever there are potentially dangerous edges and drops in a facility — be it at the lip of a loading dock or the upper level of a warehouse — you should be thinking about environmental safeguards for workers in the area. Often, these will include guard rails and other barriers, key safety awareness tools required by authorities. Warehouses, distribution centers and other industrial facilities are at their best when safety awareness is well-maintained.
Reducing avoidable accidents and their resulting injuries comes with long-lasting benefits such as good morale and worker satisfaction. Considering the importance of guard rail systems and related equipment, it’s worth looking at your own facility as soon as possible to ascertain its current protective equipment setup and potential for improvement. Then, it’s time to find ideal new assets for your needs and secure professional installation and maintenance.
GUARD RAIL USE AND OSHA SAFETY AWARENESS
An assessment of guard rail usage can begin by checking current equipment against OSHA standards. OSHA requires facilities to have fall protection systems for walking surfaces that are more than four feet above the next level down. This encompasses a wide variety of areas, including:
- Loading docks.
- Wall openings, such as chute entrances.
- Ramps and runways.
- Holes in walking surfaces, including roof skylights.
While guard rails are just one of the fall protection systems suggested by OSHA, the others are more suitable for temporary work environments and longer drops. These alternatives include safety nets and personal fall protection systems attached to workers’ personal equipment. This leaves guard rails as the obvious choice for permanent installation around edges higher than four feet, or anywhere that requires the segregation of vehicle and foot traffic.
For example, pedestrian walkways separating forklift traffic from pedestrian activity are good places for warehouse guard rail installation. OSHA does not just require a guard rail system; the agency also specifies what physical form these assets should take to reduce the danger that people may fall over or through them. These OSHA safety guard rail specifications include:
- Top rail between 39 and 45 inches above the walking surface, though it may be taller if other requirements are met.
- Panels, meshes, screens or other objects between the surface and the top rail unless there is a wall at least 21 inches high involved.
- Midrails halfway between the top edge and the walking surface.
- Openings of no more than 19 inches between protective members.
- Ability to withstand 200 pounds of force within 2 inches of the top edge without failure.
- Midrail panels and members that can withstand 150 pounds of force.
- Smooth surfaces to protect against punctures, lacerations and snagged clothing.
- No rail overhang of terminal posts if it would pose a risk.
There are also regulations about which materials are acceptable for use in rails, posts and other parts of the systems, as well as how wide in diameter those rails should be. When installing guard rails on ramps and runways, facility owners have to make sure to protect all otherwise-unprotected sides of the walking surface. While there are many OSHA regulations, they largely add up to a common-sense approach to guard rails. When these assets are built to specifications and installed correctly, they form an essential piece of a facility’s safety awareness program.
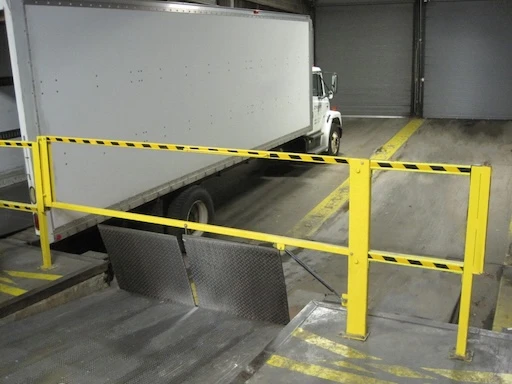
Start Right Now!
Start Right Now!
TYPES OF WAREHOUSE GUARD RAIL AND HAND RAIL SYSTEMS
Some areas of the warehouse do not require full-scale guard rails, but still demand some type of handhold that will make it easier for employees to traverse that space. In addition to standard guard rails, OSHA maintains two related categories, hand rails and stair rail systems. By determining what makes these latter two kinds of assets unique, you can find where in your facility they are required and ensure they are up to standards. As described by Oregon OSHA, these asset types are defined by the following traits:
What they are: Rather than acting to keep people or objects away from open edges, hand rails are explicitly designed to offer support as individuals walk down a slope or a staircase.
Unique requirements: As with guard rails, OSHA requires hand rails to resist 200 pounds of directly applied force. These rails must also have smooth surfaces and not project in a way that could cause injury. Since the purpose of a hand rail is to be held, these assets must be grasped. Hand rails on staircases are not the same as stair rails. While the latter guard against falls, hand rails are for holding on the way down or up. Staircases with at least four risers and three treads must have one hand rail, those wider than 44 inches must have two. If the staircase is wider than 88 inches, there must be a hand rail down the middle.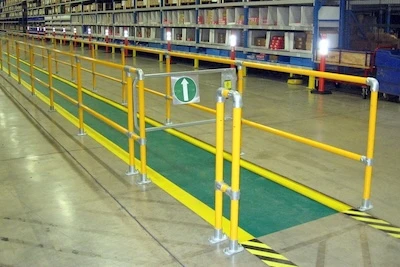
What they are: Stair rails offer the same functionality as guard rails — ensuring there are not unguarded drops — and they are installed on the exposed sides of stairways. These safety barriers are installed in tandem with hand rails, to make sure staircases have both fall protection and support. Unique requirements: OSHA changed the requirements around stair rails effective at the beginning of 2018. While the previous minimum height was 30 inches from top rail to stair tread, that number is now 42 inches. The top rail of stair rails can no longer serve as a hand rail — if an asset is meant to combine stair rail and hand rail functionality, there must be a separate rail installed for people to hold, between 30 and 38 inches high. As with guard rails, stair rails should not have openings bigger than 19 inches, and they should withstand force of 200 pounds.
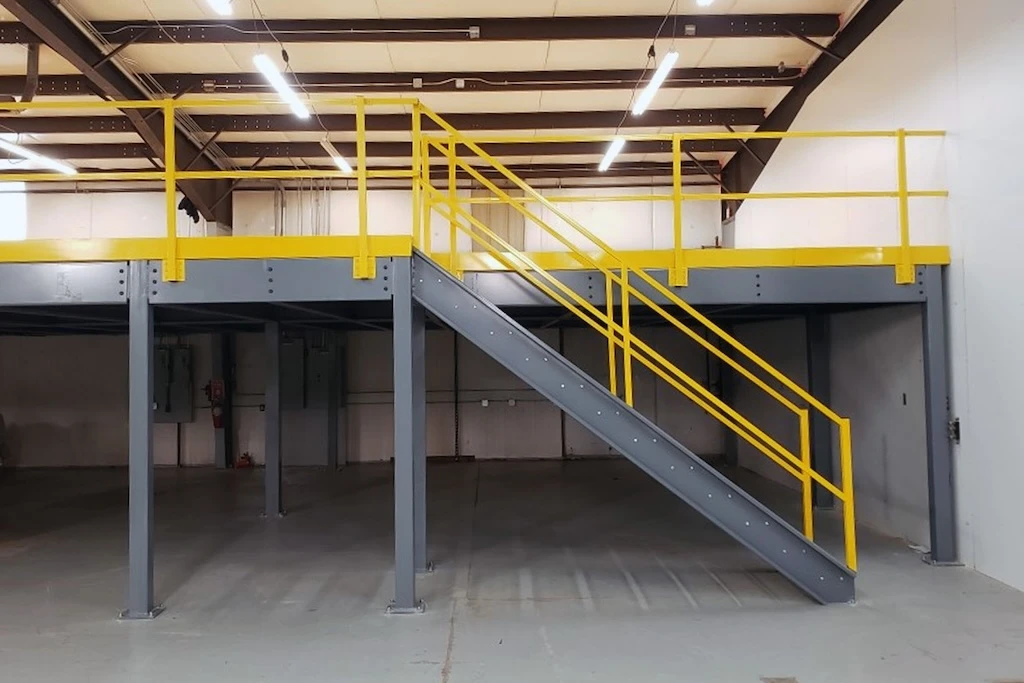
Other important equipment to install around trailer restraints includes loading dock bumpers, as well as barriers to mark the edge of the loading dock and wheel chock sets to further reduce the risk of roll-away accidents.
THE VALUE OF GUARD RAIL MAINTENANCE AND UPKEEP
The industrial safety rails around your warehouse have to be in top condition to reach their full potential. After all, degraded integrity due to age or heavy use could compromise the value and reliability of these assets. There are multiple kinds of value tied up in keeping up with maintenance for all warehouse equipment, each of which would be worth pursuing on its own. The most significant kind of return on investment from safety railing systems — such as guard rails, hand rails and stair rails — comes from the simple fact that every organization should seek to operate an accident-free workplace.
A single avoidable workplace incident is a potentially traumatic event for all personnel involved, meaning that safety awareness efforts must always be a top priority. Adequate and well-maintained heavy duty guard rail systems are there for a reason: To protect against avoidable falls and collisions. It’s in an organization’s best interests to always keep these assets working as intended.
The secondary benefit of maintenance and upkeep for safety railing and related assets around the loading dock and warehouse in general comes from minimizing supply chain disruptions. Assets that fail don’t just risk harming personnel. They can slow logistics operations, potentially causing thousands of dollars in losses for every hour that a part of the facility is unusable.
The need to stop equipment failures whenever possible is a strong incentive to invest in proactive maintenance and inspections for all assets within the warehouse. The integrity of your guard rail system should be verified often by experts, rather than taking the chance of finding a problem during an OSHA inspection — or because an asset failed.
Warehouse guard rails cannot be a “set and forget” solution that are installed and not thought of again. Fortunately, facility partners such as MINER can assist at every step of the equipment life cycle, from initial selection to ongoing maintenance.
GUARD RAIL SERVICES OFFERED BY MINER
When you work with a trusted consulting, installation, maintenance and repair organization, you can manage your facility confidently, knowing your assets are in good hands. This is the value MINER offers, affecting all warehouse equipment. When dealing with an asset as important as guard rail systems, it’s especially vital to have experts on your side.
FIND A LOADING DOCK REPAIR PROVIDER NEAR YOU
FIND A LOADING DOCK REPAIR PROVIDER NEAR YOU
COMBINING GUARD RAILS AND OTHER SAFETY AWARENESS ASSETS
While guard rail systems are a required and useful part of your warehouse safety awareness program, it’s important to remember that there are other pieces of equipment to focus on. The following are a few of the other top systems to consider:
These design elements are intended to help employees with spatial awareness while working on the loading dock and warehouse floor. Bright tape marks or painted designs, potentially paired with warning textures can help employees know when they are approaching a staircase or edge of the loading dock on foot or in a forklift.
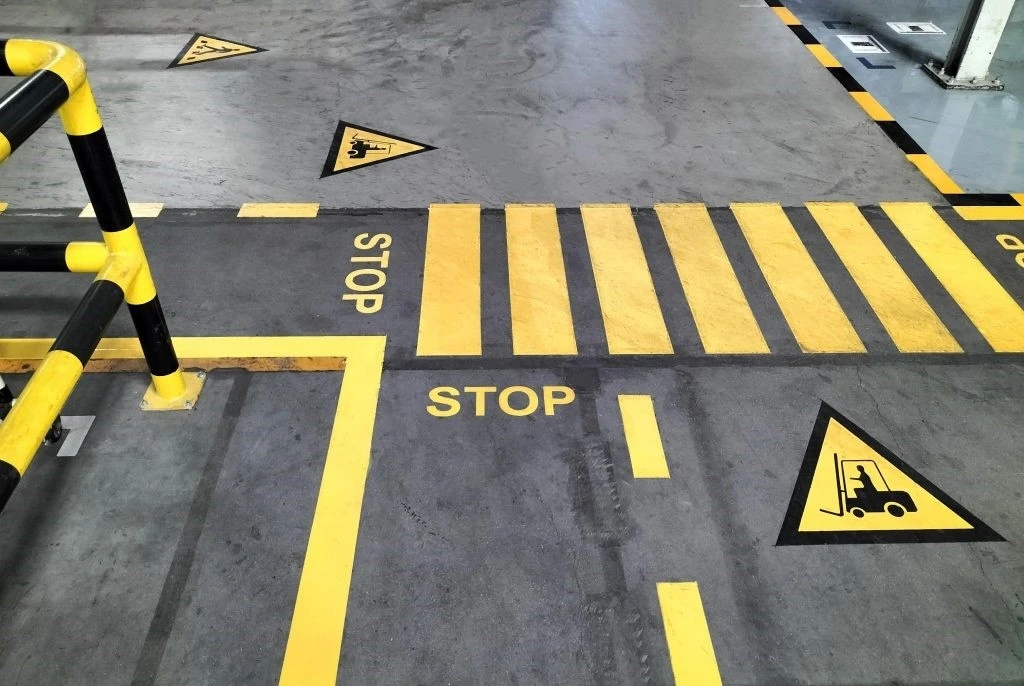
On the loading dock, vehicles pose a special risk. To limit the risk of an avoidable roll-away incident, you should install and maintain vehicle restraint assets.
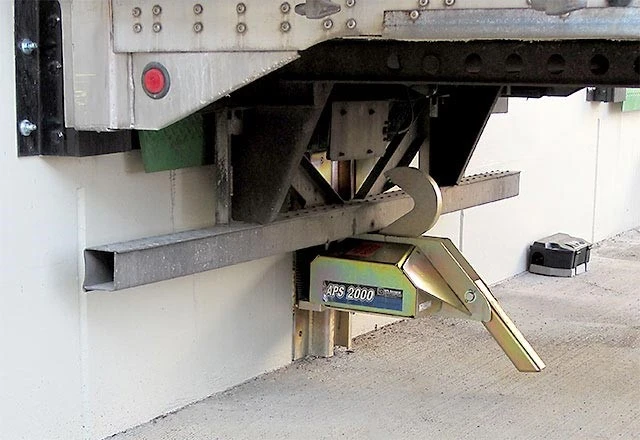
When supervisors know the status of assets such as warehouse doors and truck restraints, they can help the whole team stay aware of potential risk. This high-level view comes from connecting powered assets to a centralized control panel.

When combining assets such as these with responsibly deployed and actively maintained industrial safety railings, it’s easier to inspire confidence in your employees that you take their well-being seriously.
SELECTING, INSTALLING AND MAINTAINING EQUIPMENT
MINER’s experts are available whenever in the equipment upkeep process you need them. This can mean consulting assistance to assess your current assets and select new hardware from top vendors. It may also involve professional installation, to ensure the warehouse equipment is sound from the beginning.
Over time, proactive maintenance can be the key to ensuring every asset is delivering a maximized life span and optimized total cost of ownership. An ideal program involves frequent assessments of every asset, determining suitability, age and condition to create a hierarchy of repair urgency. With a program designed in tandem with MINER experts, you get ideal performance from essential equipment such as your guard rail system.
While proactive maintenance is intended to minimize material handling equipment downtime, sometimes emergency repairs are necessary. MINER assists with this part of the process as well, dispatching trained technicians carrying the right tools and parts to get your facility running again quickly.
Safety awareness and overall efficiency in your warehouse depend on the status of your equipment. By partnering with your organization, MINER delivers the reliability you need.
Our MinerCARE® Safety & Service Programs help you increase facility uptime, reduces total cost of ownership and ensures safety and sustainability for you and your employees. Learn more about our comprehensive MinerCARE programs that includes two distinct components: SafeCHECK and SafeACT.
AT A GLANCE: FREQUENTLY ASKED QUESTIONS
WHERE DO YOU NEED GUARD RAILS?
The Occupational Safety and Health Administration (OSHA) requires fall protection systems at the edges of all surfaces with a drop of four or more feet. Guard rails represent the simplest permanent fall protection option for your warehouse or other facility.
WHAT ARE THE OSHA REGULATIONS FOR GUARD RAILS?
OSHA regulates both the height of railings and the amount of force these assets can withstand. For example, in most cases, the top rail should be between 39 and 45 inches above the surface, with midrails and other protective features between that top rail and the surface. The rail should be able to withstand 200 pounds of force within two inches of its top, and the midrail should be able to withstand 150 pounds of force.
WHAT ARE THE DIFFERENCES BETWEEN STAIR RAILS AND HAND RAILS?
There are two separate types of railing systems needed on stairs. Stair rail systems are functionally the same as guard rails, preventing unguarded drops from the sides of staircases. Hand rails don’t fulfill the same function as guard rails — they’re meant to provide support and stability as individuals walk up and down the stairs, and they’re deployed in tandem with stair rails.
HOW DO YOU OPTIMIZE USE OF GUARD RAIL EQUIPMENT?
Guard rail assets shouldn’t be a set-and-forget piece of equipment in your warehouse. For both safety and cost-effectiveness reasons, it pays to install guard rails in partnership with an expert national service provider that can also deliver ongoing proactive maintenance. This continued attention helps you detect potential issues and reduces the chance of a dangerous failure or OSHA penalty.